The Precision of CNC Machines: Revolutionizing Metal Fabrication
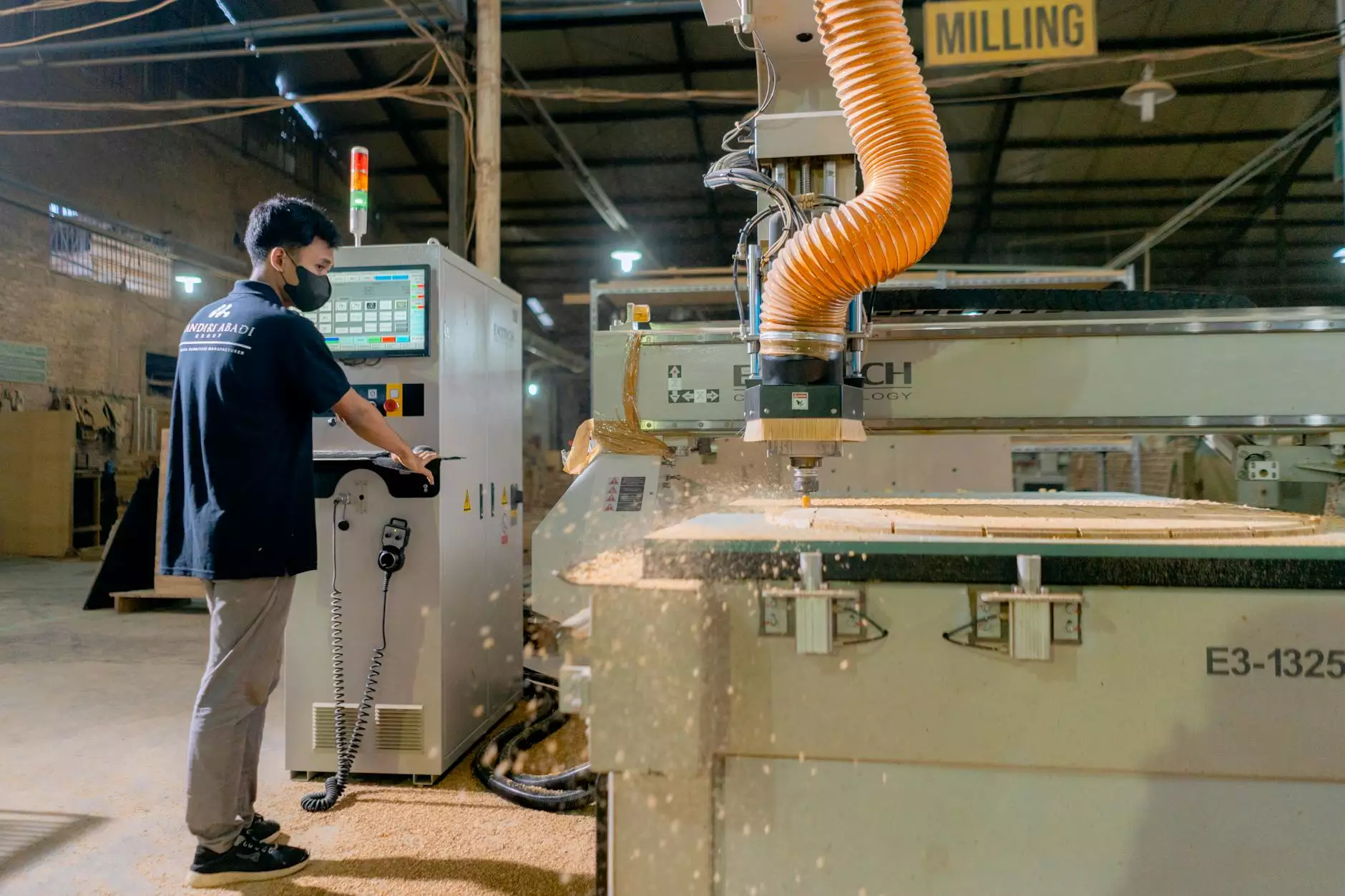
In the contemporary landscape of manufacturing, the precision of CNC machines stands as a pivotal cornerstone in the quest for efficiency, quality, and versatility. As industries relentlessly pursue higher standards of craftsmanship, the role of CNC (Computer Numerical Control) technology in metal fabrication becomes increasingly paramount. This article delves deep into the intricacies of CNC machining, emphasizing its importance for metal fabricators, and articulating how these machines are transforming the production ecosystem.
Understanding CNC Machines
CNC machines are automated milling devices that use computer programming inputs to dictate the movement and operation of tools. They provide extraordinary accuracy and repeatability, making them ideal for tasks that require meticulous attention to detail. Whereas traditional machining processes rely heavily on manual input and skilled operators, CNC automation facilitates a new era of production where precision meets speed.
Types of CNC Machines
Various types of CNC machines exist, each tailored for specific tasks within the metal fabrication sector. Here are some of the most common:
- CNC Mills: Used for cutting and shaping materials by removing metal from the workpiece.
- CNC Lathes: Designed for shaping materials by rotating the workpiece while cutting tools are applied.
- CNC Plasma Cutters: Utilize high-velocity jets of ionized gas to cut through metal sheets.
- CNC Lasers: Use focused laser beams to cut or engrave highly intricate designs.
- CNC Waterjet Cutters: Employ high-pressure water jets mixed with abrasives to cut materials in delicate and precise manners.
The Importance of Precision in Metal Fabrication
The precision of CNC machines is essential not just for aesthetic integrity, but also for the functional performance of the final products. Here’s why precision is paramount in metal fabrication:
- Quality Control: High precision means less waste and fewer defects, thus maintaining consistent product quality.
- Cost Efficiency: Minimizing errors reduces material waste and lowers labor costs, allowing businesses to maximize their profitability.
- Complex Design Capabilities: CNC machines can produce intricate designs that are impossible to achieve with manual tooling.
- Speed of Production: Automated processes lead to faster production times, meeting market demands effectively.
The Advantages of Using CNC Technology in Metal Fabrication
Embracing CNC technology in metal fabrication provides businesses with numerous advantages. Here are some of the most salient benefits:
Enhanced Accuracy and Precision
One of the most significant benefits of CNC machining is its unparalleled accuracy. CNC machines are capable of producing components that adhere to tolerances of just a few microns. This level of precision is essential in industries such as aerospace, automotive, and medical devices, where even the slightest deviation can result in catastrophic failures.
Greater Flexibility and Customization
The adaptability of CNC machines allows metal fabricators to execute both high-volume production runs and custom one-off projects with ease. With the ability to alter designs swiftly, businesses can respond promptly to market demands and customer preferences.
Improved Efficiency
CNC machines operate continuously, vastly increasing production rates. Once programmed, they can work autonomously, reducing the need for operator involvement. This not only accelerates production but also allows skilled technicians to focus on more complex tasks.
CNC Machining Processes in Metal Fabrication
To fully grasp the *precision of CNC machines*, it’s essential to understand the various processes involved in metal fabrication.
Machining
This process includes several sub-processes such as turning, milling, drilling, and grinding. Each has its technique and application, but they all share the goal of removing material to achieve the desired shape and finish.
Welding
CNC technology has also extended into welding applications, where precision welding techniques (such as laser and TIG welding) ensure strong, durable joints in metal assemblies. This technological integration boosts overall production efficiency while maintaining quality standards.
Sheet Metal Fabrication
Processes such as cutting, bending, and stamping utilize CNC systems to achieve complex shapes and designs in sheet metal. This segment is particularly crucial for industries such as construction, automotive, and consumer equipment.
The Future of CNC Machining in Metal Fabrication
As technology evolves, so too does the capability of CNC machines. The future of metal fabrication will likely see even greater innovations in automation, including:
Integration of AI and Machine Learning
The incorporation of artificial intelligence into CNC programming could lead to self-optimizing machining processes that adapt in real time based on material behavior and environmental conditions.
Vertical Integration of IoT
The Internet of Things (IoT) will facilitate real-time monitoring and data exchange for CNC machines, providing insights into production processes, machine health, and predictive maintenance schedules.
Expanded Materials Capabilities
With ongoing research and development, CNC machines are progressively being designed to work with a wider array of materials, including composite materials and advanced alloys, thereby broadening their application horizons.
Challenges Facing CNC Machining
Despite its numerous benefits, the precision of CNC machines does not come without challenges:
Skill Gap
As operations become more complex, there’s a mounting need for qualified technicians who can program and maintain CNC systems. The industry must focus on attracting talent and providing adequate training to meet this demand.
High Initial Investment
While CNC machines reduce costs in the long term, the initial investment can be substantial. This financial barrier may deter smaller businesses from modernizing their operations. However, various financing options are available to help mitigate this challenge.
Maintenance and Upkeep
CNC machines require regular maintenance to ensure optimal performance. Neglecting this aspect can lead to downtime, which can significantly impact production schedules and profitability.
Conclusion
Embracing the precision of CNC machines is essential for any business in the metal fabrication industry looking to remain competitive. From enhanced accuracy and improved efficiency to increased flexibility and the ability to produce complex parts, CNC technology is undoubtedly reshaping the future of manufacturing.
As we move forward, adopting new technological advancements and addressing current challenges will be crucial for unlocking the full potential of CNC machining. Companies like DeepMould are leading the charge in this evolution, setting standards that inspire future innovations in metal fabrication. In doing so, they exemplify how precision engineering can harmonize with modern manufacturing to create superior products and drive business success.