The Essential Role of **Injection Molding Tools** in Modern Metal Fabrication
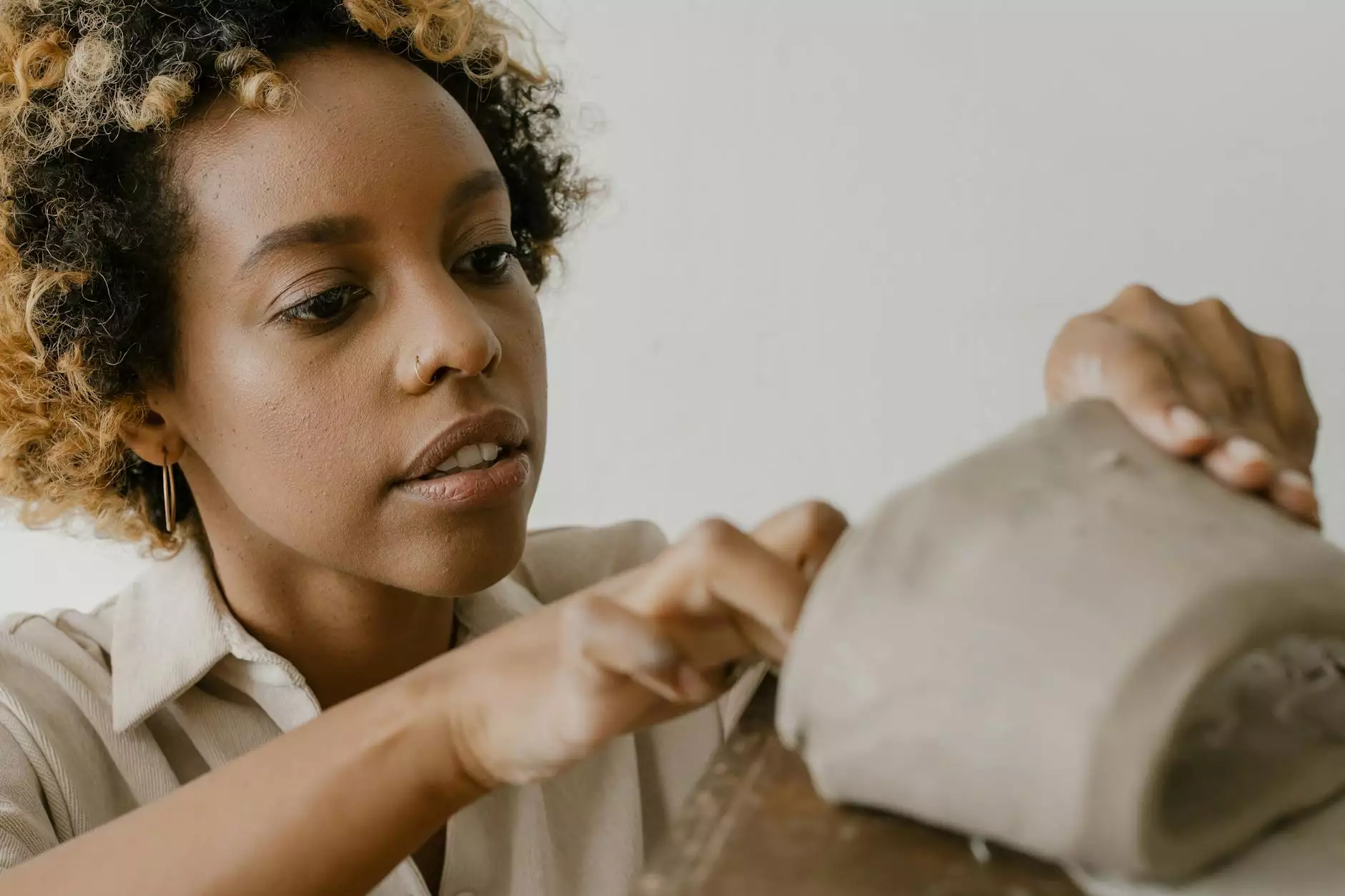
In the rapidly evolving landscape of manufacturing, the injection molding tool has emerged as a critical component in the production process. As businesses seek to enhance efficiency while maintaining high standards of quality, understanding the intricacies of injection molding becomes paramount. This article delves deep into the world of injection molding tools, examining their advantages, applications, and future potential within the context of metal fabrication.
What is an Injection Molding Tool?
An injection molding tool is a vital device used in the injection molding process, a manufacturing method for producing parts by injecting molten material into a mold. This process is predominantly employed for metals, plastics, and other materials, making it a cornerstone of modern manufacturing. The molds used in this process are engineered to create specific shapes and sizes, ensuring consistency and precision across mass-produced components.
Components of an Injection Molding Tool
Understanding how injection molding tools work requires a closer look at their individual components. Here are the primary elements:
- Mold Base: The foundation of the injection molding tool, providing support for the mold cavities.
- Mold Cavity: The hollow space within the mold where the molten material is injected to form the part.
- Ejector System: A mechanism that removes the finished part from the mold once it has solidified.
- Cooling Channels: Integrated pathways that allow coolant to circulate in order to control the temperature of the mold during the injection process.
- Injection Unit: The part of the machinery responsible for melting and injecting the material into the mold cavity.
Advantages of Using Injection Molding Tools
The use of injection molding tools in metal fabrication comes with numerous benefits that enhance production efficiency and product quality:
1. High Precision and Consistency
Injection molding tools are designed for precision, allowing for the production of complex shapes and details with a high degree of accuracy. The injection molding process ensures that each part produced is consistent in quality, size, and shape, a crucial factor in industries where precision is non-negotiable.
2. Efficient Production Rates
One of the most significant advantages of using an injection molding tool is its ability to produce large quantities of parts in a relatively short timeframe. This efficiency drastically reduces lead times, making it an ideal choice for high-volume production runs.
3. Cost-Effectiveness
While the initial investment in injection molding tools can be substantial, the long-term savings are significant. The rapid production rates, coupled with reduced material waste and labor costs, make this manufacturing technique highly cost-effective over time.
4. Versatility
Injection molding tools can work with a wide range of materials, including various metals and plastics, making them versatile for different applications. This adaptability is essential for manufacturers looking to diversify their product offerings.
Applications of Injection Molding Tools in Metal Fabrication
The applications of injection molding tools in metal fabrication are vast and varied, demonstrating their importance across several industries:
1. Automotive Industry
In the automotive sector, injection molding tools are utilized to produce intricate components such as dashboard panels, casings, and engine parts. The ability to create lightweight yet durable parts leads to increased fuel efficiency and better overall vehicle performance.
2. Aerospace Industry
The aerospace industry heavily relies on precision-engineered components, and injection molding tools provide the necessary accuracy and reliability. Parts produced using this method are often subjected to rigorous testing standards to ensure safety and performance.
3. Consumer Electronics
From smartphones to household appliances, consumer electronics benefit from the use of injection molding tools. The ability to create sleek, compact designs aids companies in meeting consumer demand for aesthetically pleasing and functional products.
4. Medical Devices
In the medical field, exacting standards are essential. Injection molding tools produce precise, clean parts suitable for medical devices. This technology also enables the production of complex components that may be difficult to achieve with other manufacturing methods.
The Future of Injection Molding Tools
The future of injection molding tools appears bright as technology continues to advance. Several trends are emerging that are likely to influence the industry significantly:
1. Automation and Smart Manufacturing
The integration of automation and smart technologies into the injection molding process enhances efficiency and reduces operational costs. Automated systems allow for faster changeovers between production runs, minimizing downtime and enhancing overall productivity.
2. Eco-Friendly Materials
As businesses strive for sustainability, there is a growing trend toward using eco-friendly materials for injection molding. Innovations in bioplastics and recycled materials are paving the way for greener manufacturing practices.
3. Additive Manufacturing Integration
The merging of additive manufacturing techniques with injection molding can lead to even more sophisticated production capabilities. This fusion allows for more complex designs and the possibility of creating molds that would be impractical using traditional methods.
Conclusion: The Impact of Injection Molding Tools on Metal Fabrication
The importance of injection molding tools in the realm of metal fabrication cannot be overstated. Their ability to produce high-quality, precise components quickly and efficiently makes them invaluable in multiple industries. As innovation continues to shape the manufacturing landscape, those who adapt and optimize their processes with advanced injection molding tools will find themselves at the forefront of the market.
To learn more about how injection molding tools can benefit your business, consider reaching out to expert providers like DeepMould.net, a leader in the field of metal fabrication. By implementing these advanced technologies, you can take your manufacturing processes to the next level, ensuring quality, efficiency, and sustainability in your operations.